Technology
Makingit innovative
Fine packaging solutions should combine such features as high functionality and supreme design. Our creative product development dept. as well as the modern automated machinery park work together on putting those two elements into a single product available in our offer.
Technology
Fine packaging solutions should combine such features as high functionality and supreme design. Our creative product development dept. as well as the modern automated machinery park work together on putting those two elements into a single product available in our offer.
Makingit innovative
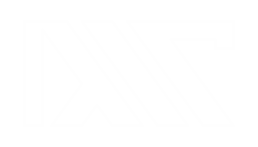
Royalpack is the one and only company in Europe that has a unique corrugated board production line with various innovative technological solution, which is able to laminate the product at once.
New generation large-format printing machines produce excellent high-resolution offset or flexo print on the substrates that we use. Other processing equipment, such as automatic die cutters for corrugated cardboard and solid board are able to produce even the most complex structures with high precision. Last but not least, there are our advanced folding and gluing lines which close the packaging block by the means of hot melt glue, low melt glue, pressure sensitive adhesives, staples or specialistic adhesive tapes. Ultimately, the packaging offered by Royalpack becomes an effective marketing tool for the customers who have trusted us, which we also are proud of.
Offset printing
Offset printing is the perfect solution for the most demanding graphic projects. It not only provides high quality of the overprint, but above all, it gives the best possibilities when it comes to refining. Royalpack is equipped with a new generation large-format offset printing machine, thanks to which it can produce the following finishing:

Standard, with CMYK ink, Pantone and dispersion varnish
Food ink
Fluorescent ink
Metallic ink
Print on PE+PET layer
Food varnish
Soft-touch varnish
Anti-slip varnish
UV varnish
Selective varnishes, e.g. matte primer + UV
Primer varnishes for foil lamination, e.g. metallic
We have introduced the unique packaging series called NATURA LINE, in offset printing. It is designed for precise printing of uncoated brown paper, as well as grass paper and thus offering our customers the chance to choose sustainable products. We believe that offset printing does not have to be associated exclusively with coated bleached paper. We are proud to present pro-ecological solutions along with the most unique packaging solutions allowing products to be effectively advertised in stores.
Offset Printing
Offset printing is the perfect solution for the most demanding graphic projects. It not only provides high quality of the overprint, but above all, it gives the best possibilities when it comes to refining. Royalpack is equipped with a new generation large-format offset printing machine, thanks to which it can produce the following finishing:
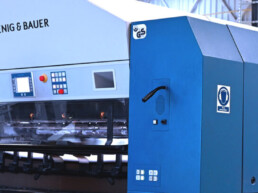
Standard, with CMYK ink, Pantone and dispersion varnish
Food ink
Fluorescent ink
Metallic ink
Print on PE+PET layer
Food varnish
Soft-touch varnish
Anti-slip varnish
UV varnish
Selective varnishes, e.g. matte primer + U
Primer varnishes for foil lamination, e.g. metallic
We have introduced the unique packaging series called NATURA LINE, in offset printing. It is designed for precise printing of uncoated brown paper, as well as grass paper and thus offering our customers the chance to choose sustainable products. We believe that offset printing does not have to be associated exclusively with coated bleached paper. We are proud to present pro-ecological solutions along with the most unique packaging solutions allowing products to be effectively advertised in stores.
Flexographic Printing
Flexographic print has earned its place among printing methods recently. Undoubtedly, thanks to the ongoing work of R&D teams of large-format printing machine makers, the quality of this type of printing has reached high level. Its major advantage is the ability to print directly on the cardboard’s sheet, which allows for.

Grammage reduction of particular layers of corrugated cardboard
Shortening the order fulfilment time by eliminating the laminating process
Packaging cost optimization
Thanks to the hi-tech large-format flexographic machine and the fact that we produce cardboard by ourselves, we have real and full influence on the quality of the offered packaging.
Royalpack understands that machines are not everything. The people who you work with are the most important. Our printing staff are masters of their profession. Thanks to them and to cooperation with well-known material suppliers of paper, ink and photopolymers (plates), we are able to carry out the most demanding projects.
Flexographic printing
Flexographic print has earned its place among printing methods recently. Undoubtedly, thanks to the ongoing work of R&D teams of large-format printing machine makers, the quality of this type of printing has reached high level. Its major advantage is the ability to print directly on the cardboard’s sheet, which allows for.
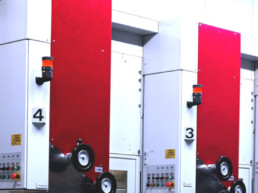
Grammage reduction of particular layers of corrugated cardboard
Shortening the order fulfilment time by eliminating the laminating process
Packaging cost optimization
Thanks to the hi-tech large-format flexographic machine and the fact that we produce cardboard by ourselves, we have real and full influence on the quality of the offered packaging.
Royalpack understands that machines are not everything. The people who you work with are the most important. Our printing staff are masters of their profession. Thanks to them and to cooperation with well-known material suppliers of paper, ink and photopolymers (plates), we are able to carry out the most demanding projects.
Barriers
We aim at sustainable growth. Our goal is to limit the use of synthetic materials in the production of packaging while adjusting the processes to meet ecological standards at the same time. How to secure a product against moisture, grease and savour? The answer is simple: barrier solutions - biodegradable and food-grade.
Transparent PET foil is used for securing the cardboard’s surface (e.g. protecting the content of the packaging from the inside so that it does not go outside). This method is similar to laminating with BOPP foil, except for the fact that PET foil has high surface tension and can be glued by a folding – gluing machine.


Our waterproof and grease-resistant barriers are used in various areas.

For fast food products such as hamburgers or pizza.

For dishes that require heating up, e.g. in a microwave oven.

For products being prepared in the oven.

For food stored in a freezer.

For hot drinks providing high cup protection.

Our waterproof and grease-resistant barriers are used in various areas.

For fast food products such as hamburgers or pizza.

For dishes that require heating up, e.g. in a microwave oven.

For products being prepared in the oven.

For food stored in a freezer.

For hot drinks providing high cup protection.
Our barrier solutions are thermo-active, which allows to glue layers of paper together through temperature and pressure – without using extra hot melt glue. We can adjust the amount of material in order to obtain the perfect barrier and permeability proportions for a particular product. Thanks to the wide barrier customization spectrum, we are able to create packaging perfectly matching the end product. We all work for ecological solutions and a sustainable future together.

Refinements
Packaging is not only defined as a way of protecting the goods, but above all, it creates the product brand. Refinements work best among offset-printed packaging and those made of solid board in particular. We offer the following refinements:
Varnish: dispersion, gloss dispersion, matte, soft touch, ant-slip, structural and other
Ink: standard, metallized, fluorescent and other
Foil: gloss, matte, soft touch, anti-scratch, metallized and other
Selective hot-stamping
Embossing: concave, convex
Window: PET foil used in window box packaging
